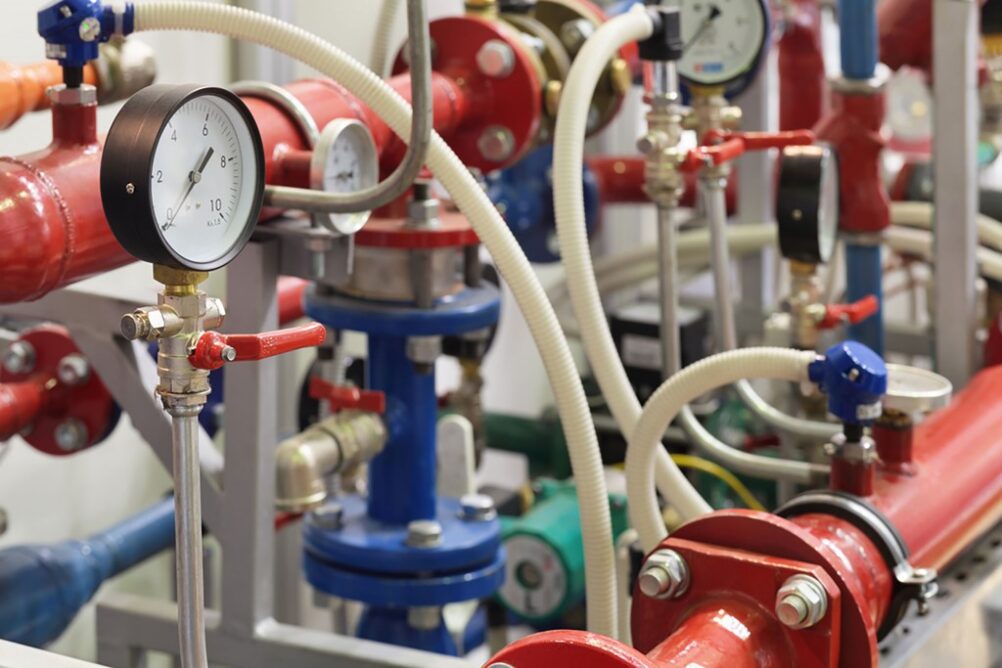
The Problems
- Air consumption reaching maximum capacity for the compressors.
- Electrical costs of running compressors at full capacity.
- Pump failure rates due to 24/7 operation.
- System downtime to replace pumps.
- High wear due to abrasive nature of products.
The Solution
After extensive study of the applications the following recommendations were made.
- Where possible increase the pumps from 2” to 3” ported.
- Modify pipework to remove sharp bends and elbows allowing easier flow of material.
- Install compressor control system to maximise efficiency of the current 4 existing compressors.
- Instigate service exchange programme to ensure repaired pumps are always ready for use.
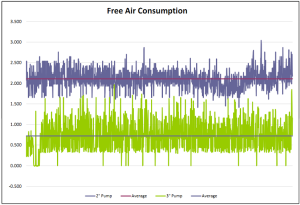
The Result
The graph illustrates the actual results the client recorded during a trial. A 2” and then a 3” pump were mounted on the same application and regulated to the same flow capacity for a 1 week period.
- By using 3” pumps, the air consumption dropped to 1/3 of a 2” pump, effectively running three pumps for the price of 1.
- By modifying pipework, resistance was decreased meaning less pressure required to pump product, this meant pumps could be turned down saving huge amounts of air.
- As a 3” pump displaces double the volume of a 2” pump, The reduced number of flexes and the lower liquid velocity extended maintenance intervals way beyond previous levels.
- Utilising our service exchange program and test facility, no unnecessary spares were fitted, this reduced the parts costs per repair by over 50%
- The client realised a £70k maintenance saving in the first year working with DPGOC.